Selection and Suggestion of Filter Paper for EDM Filters
EDM machine tools are mainly used for the manufacture of various molds, electrodes, and precision parts, as well as the processing of complex cavities and curved surfaces of various conductive materials. It has the characteristics of high machining accuracy, high finish and fast cutting speed. Especially in medium-speed wire cutting machine tools and low-speed wire EDM machine tools, the filter plays a vital role in ensuring processing accuracy and stability. Now combined with TAGUTI EDM FILTER's 15 years of experience in filter manufacturing, let's analyze the selection and suggestions of filter paper.
1. The materialof filter paper
It uses mixed wood pulp, including: softwood pulp, hardwood pulp, dragon's whisker pulp, etc.
2. The performance of filter paper
- Bulkiness of filter paper: Only fluffy can be breathable, the density is 0.15 ~ 0.35g/cm³, high alpha fiber;
- Aperture of filter paper: The filter paper has small aperture and large number of perforations per unit area, which can filter out fine particles, is suitable for precision machining; The one has large aperture, small number of perforations per unit area, which is suitable for rough machining;
The following parameters are commonly used: maximum aperture, average aperture.
- Air Permeability of filter paper: Air permeability under 1mmH₂O pressure>80L/m²/s;
- Burst Strength: >250Kpa;
- Stiffness: > 6Mn.m.
3. The structure of filterpaper
- The filter paper is directional, the fibers on the front of the filter paper are loose while the fibers on the reverse side are tight, the pores on the front are in the shape of a bell mouth, and the pores become smaller along the thickness direction of the filter paper.
- The thickness of filter paper: About 0.25~0.40mm;
- The whole thickness of filter paper (including the depth of the corrugation): about 0.40 to 0.70mm;
- The particle size of the impurity particles after electric machining discharge varies from a few microns to tens of microns;
- Filter paper filtration can not be simply understood as only the screen function, it also has the function of depth filtration, the filter paper presents a labyrinth multi-layer structure (as shown below);
- The front of the filter paper should face the direction of the working fluid, the reverse of the filter paper should be the direction of the outflow of the working fluid, and the reverse side should be marked with colored lines for easy identification by users. If the positive and negative directions are wrong, the dust storage capacity of the filter element will be reduced by more than 30%.
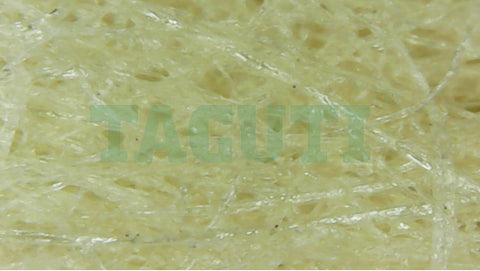
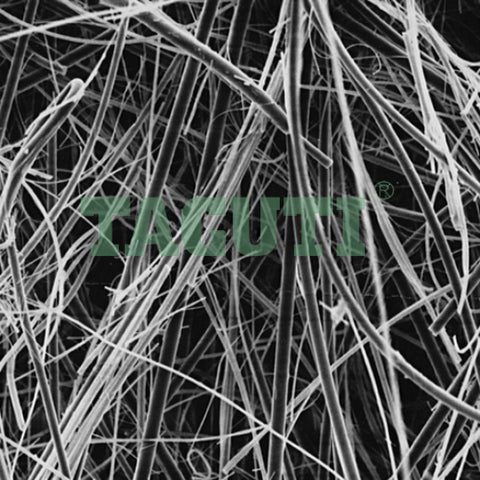
The surface structure of the filter paper after magnification 2000 times
4. The filter paper impregnated with phenolic resin
The filter paper made of mixed wood pulp is very fragile, it cannot withstand the harsh working conditions of the filter element during processing, and it is easy to break under the constant impact of the working fluid. We usually add phenolic resin to the filter paper, the resin content is 10-30%, and the physical strength of the filter paper can be increased by more than 300%. If the phenolic resin content is insufficient, the strength of the filter paper will be low; if the phenolic resin content is too high, the filter paper will become brittle and easily damaged.
5. The Curedfilter paper
The filter paper impregnated with phenolic resin has not yet hardened. After indentation and folding on the origami machine, it must be heated at 150°C for 10 to 15 minutes to cure the phenolic resin and increase the stiffness of the filter paper, then cross-linking occurs between the polymer chains to form a three-dimensional structure that improves stiffness and rigidity.
6. The non-curedfilter paper
Non-cured filter paper uses thermoplastic resin impregnation technology. Ethylene polymers are generally used, such as polyvinyl acetate resin, acrylic resin, polyvinyl chloride, butadiene-styrene latex, polyethylene acetate ester. During the processing of non-curing resin, it need only a little heat or no heating. This type of resin has a certain flexibility at room temperature and is suitable for the manufacture of oil-based electrical processing filter elements.
7. The comparison of various properties of cured and non-cured filterpaper
- The requirements of base paper material, manufacturing process, and base paper quality are almost the same, the difference is the impregnating agent and impregnation process;
- There is a certain difference between the final paper quality requirements and technical parameters;
- Physical properties, tensile strength, bursting strength, stiffness, water release performance, temperature stability, particle filtration efficiency, life, and performance at different temperatures, humidity and media.
8. Comprehensive overview
9. Filter paper for WEDM filters after use
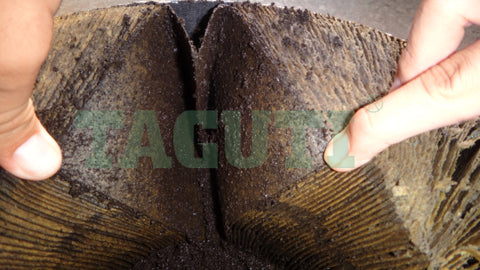
The surface of the filter paper after use
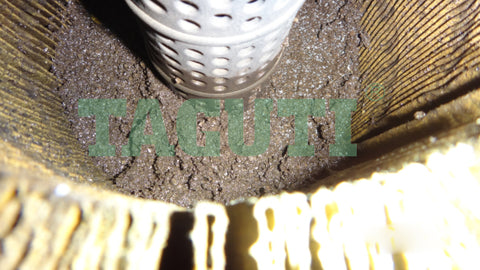
Impurities intercepted inside the filter after use
10. Summary
In the manufacturing process of EDM filters, how to choose a kind of suitable filter paper is very critical. Due to the different processing environments, processing conditions and processing techniques, no filter paper can be comprehensive. We need to find a balance point in the cost of use, service life, and use effect and get the most cost-effective products to return the majority of users.
Wire EDM Filters
- $25.50
- $25.50
- Unit price
- / per
- $25.50
- $25.50
- Unit price
- / per
- $7.50
- $7.50
- Unit price
- / per
- $33.50
- $33.50
- Unit price
- / per
- $22.50
- $22.50
- Unit price
- / per
- $22.50
- $22.50
- Unit price
- / per
- $33.50
- $33.50
- Unit price
- / per
- $25.50
- $25.50
- Unit price
- / per
- $6.95
- $6.95
- Unit price
- / per
- $32.50
- $32.50
- Unit price
- / per
- $48.00
- $48.00
- Unit price
- / per
- $32.50
- $32.50
- Unit price
- / per
- $32.50
- $32.50
- Unit price
- / per
- $32.50
- $32.50
- Unit price
- / per
- $7.95
- $7.95
- Unit price
- / per