
- May 12, 2022
The Analysis and Solution of "speckled wire" Phenomenon of EDM Molybdenum Wire
After a period of processing, the molybdenum wire EDM wire will appear dark and light-colored spots, sometimes arranged according to a certain pattern to form a pattern, so it is called "speckled wire".
1. The cause for the formation of the "speckled wire" phenomenon
Due to the inability to effectively deionize the continuous arc discharge, the resistance heat of the arc precipitates a large amount of carbon to form carbon fine particles, and the molybdenum wire itself is also carbonized. The workpiece is thick (long discharge gap), the dielectric coefficient of the EDM gel is low (poor recovery and insulation ability), and the pulse power supply has a DC component (>10mA) that delays arc extinguishing. One of these three causes is the basic conditions for the formation of "speckled wire" phenomenon.
An "impurity" that is brought into the discharge gap (or inherent in the workpiece) that affects the spark discharge is the cause of the "speckled wire" phenomenon. "speckled wire" is the same as the arc drawing and burn of spark discharge machining. Once the arc drawing and burn in the gap are formed, the workpiece and the electrode will be burned out of the pit at the same time and form carbon fine particles, the machine will not continue processing if the carbon fine particles are totally not be cleaned up. Wherever the fine carbon fine particles stick, arc burns will occur, and the area will become larger and larger,then there is no possibility of self-elimination. If the workpiece and the electrode are displaced, each and the opposite side will cause new arc burns, and one will become two.
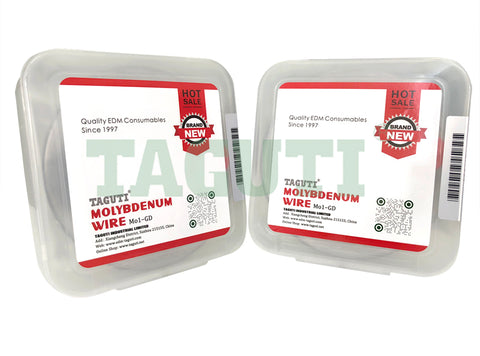
2. The Occurrence and Development of "Speckled wire"
When the discharge gap is long, the removal of corrosion products is difficult, the recovery insulation ability is poor, and the spark explosion is weak, "impurities" are easily generated, and the resistance heat rapidly changes into arcing and burns, and the carbon fine particles are also accompanied. The wire moves, during which each pulse energy is released through this arcing point, until the arcing point exits the workpiece, the insulation can be restored, and it is possible to generate a new spark discharge.The burn carbonization (black spots) of the molybdenum wire point is formed. If the point in the gap that induced the arc burn is still stubbornly existing, it is very easy to repeat the arc discharge with the molybdenum wire point in contact now, and the second burn carbonization ( black spot) point is formed again. So the distance between that point and the workpiece exit is often equal to the distance between the two black spots.
After the first burn and carbonization, a carbonization point was left on the wire, and a series of carbonization points were left in the gap between the workpieces. When the fine carbon particles were spread into the water, they would enter the gap at any time, then they all became the inducing factor of "speckled wire", which is called "cross infection". At this time, changing the molybdenum wire, the EDM gel, and the workpiece will not work, and even changing all of them will not help. After a period of time, the inducing factors of "cross-infection" are gone, the machine can normally process.
3. The Appearance and Observation of "Speckled wire"
Pulse-sourced ammeters can swing significantly due to arcing, short circuits, open circuits, and carbon fines formation. Discharge sparks will appear red, yellow, and white. The initially formed "black spot" becomes thicker due to thermal burning and carbonization, and then becomes thinner after passing through the gap and ablating several times. Of course, heating and tension for a period of time also makes the "black spots" thinner. Brittle is caused by burning red and cooling, severe carbonization. Because the pattern formed by "speckled wire" on the wire storage drum is easy to arrange regularly, many people try to find the regularity, but they find the result is wrong with the circumference of the wire cylinder, the circumference of the guide wheel, and the distance of the power feed contact. If there is a rule, it is the distance from the point of arcing and burn occurrence to the exit of the workpiece.
4. The Solution and Analysisof "Speckled Wire"
Once the phenomenon of "speckled wire" occurs, it must be solved from the three aspects of the cause.
a. First of all, It needs to confirm the quality of the pulse power supply. As long as there is no DC component that prevents arc extinguishing, it usually does not cause speckled wire.
b. Secondly, pay attention to the EDM gel. It is definitely not acceptable for it to be dirty, too dilute, or to reduce the effective components. It is also not acceptableto contain a certain amount of salt, alkali and other components that hinder the dielectric insulation.
c. Thirdly, Pay attention to the processing materials. If the materials are verythin, even if there is an incentive for arcing and burns, the exchange of the EDM gel is fast, and the removal of corrosion and impurities is easy, the wire "passes" in an instant. If the material is too thick, the causes of arcing and burns are easily generated and extremely difficult to discharge. Especially with black oxide skin, forged inter-layer, and raw materials that have been quenched without forging and tempering, the probability of causing "speckled wire" is very high.
If you need to cut this piece of processing material, you can completely change the molybdenum wire and the EDM gel. The inter-layer and quenching of the processing material cannot be changed, at least remove the oxidized black skin on the surface, avoid the gap that has been cut. Start with large pulse interval, large pulse width, small current, and high voltage, and gradually increase the current after the processing is stable.